Metallurgy Furnace
Blast Furnace
Large-scale construction of a blast furnace is often done using a shaft furnace design method. In these furnaces, iron is obtained from iron ore through reduction. Coke serves predominantly as an energy source and reducing agent. Various aggregates, such as quartz sand and lime, are used for slagging and to lower melting temperature . We have international experience in brick lining in this specialized field.
Coking Plant (Coke Oven)
Coke is produced in a coking plant with a dry distillation process. The volatile components in coal are released by heating to a temperature of 900° to 1400°C (1650° to 2550°F) and extracted by suction. The porous coke formed in this manner contains predominantly carbon and ash constituents. Coal reusable materials including tar, sulfuric acid, ammonia, naphthalene, benzol and coal gas are obtained from the crude gas.
Our employees have distinguished themselves through quality and precision of work especially in the field of coke ovens.
Converters
In various converter processes (Thomas, Bessemer and DSN), gases are squeezed into the crude iron smelter using converter floor nozzles. The Thomas and Bessemer processes use air, and in the DSN process (named after the German words for steam, oxygen and Neunkirchen) oxygen together with steam is used instead of air. The processes differ in the brick lining of the oven, which has either an acid or base effect, and therefore exhibits different properties.
We will gladly make our technical knowledge in the field of brick lining available to you.
Arc furnace (Electric Arc Furnace)
In the arc furnace process, electrical and chemical energy is used for the smelting process. Here a large portion of the energy is converted to thermal energy (to 3500°C, or 6300°F) and serves to fuse the charging material. An additional portion is used to heat the furnace lining.. An arc burns between the electrode and the charging material. The heat over it is transmitted to the charging material through radiation.
In the electric-furnace steel process, steel is produced from steel scrap and other ingredients. In addition to the molten raw steel, a slag cover on the molten mass is formed from the non-metallic ingredients and oxides of the alloy materials. This binds unwanted constituents and thus protects the chalybeate bath.
Our specialized oven manufacturers are equipped with the most up-to-date tools and are happily available to consult with you.
if ($id==3){ ?>
Get the Flash Player to see this player.
} if ($id==5){ ?>
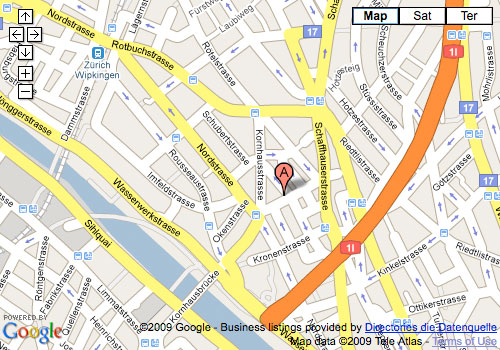
see large map } ?>